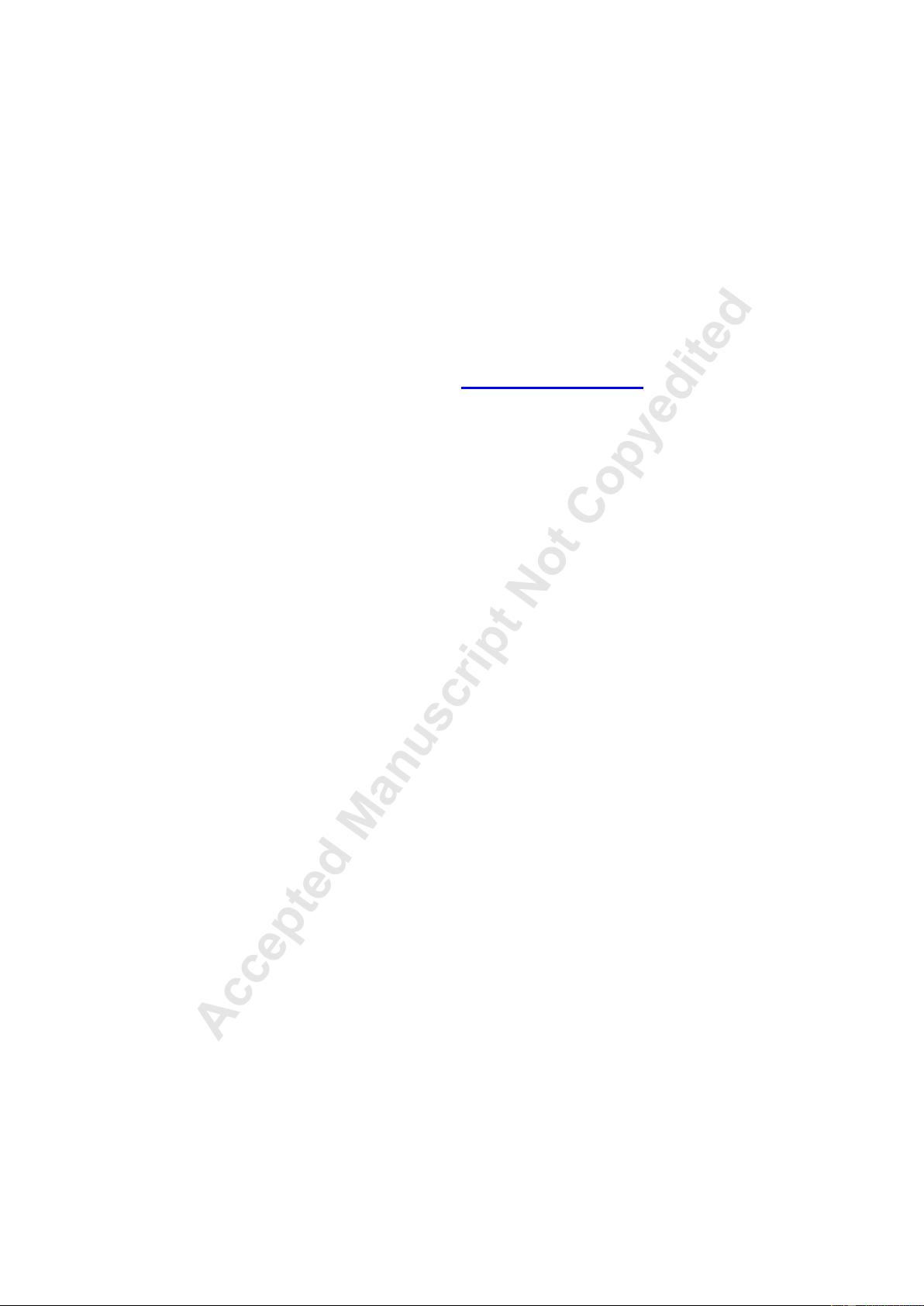
1
A numerical model to study the role of surface textures at TDC reversal in
the piston ring to cylinder liner contact
N. Morris
1
, R. Rahmani
1*
, H. Rahnejat
1
, P.D. King
1
and S. Howell-Smith
2
1
Wolfson School of Mechanical and Manufacturing Engineering, Loughborough
University, Leicestershire, UK
2
Capricorn Automotive Ltd, Basingstoke, UK
*Corresponding author: R.Rahmani@lboro.ac.uk
Abstract
Minimisation of parasitic losses in the internal combustion engine is essential for improved
fuel efficiency and reduced emissions. Surface texturing has emerged as a method palliating
these losses in instances where thin lubricant films lead to mixed or boundary regimes of
lubrication. Such thin films are prevalent in contact of compression ring to cylinder liner at
piston motion reversals because of momentary cessation of entraining motion. The paper
provides combined solution of Reynolds equation, boundary interactions and a gas flow
model to predict the tribological conditions, particularly at piston reversals. This model is
then validated against measurements using a floating liner for determination of in-situ friction
of an engine under motored condition. Very good agreement is obtained. The validated model
is then used to ascertain the effect of surface texturing of the liner surface during reversals.
Therefore, the paper is a combined study of numerical predictions and the effect of surface
texturing. The predictions show that some marginal gains in engine performance can be
expected with laser textured chevron features of shallow depth under certain operating
conditions.
Keywords: Internal combustion engine; surface texture; piston ring; friction; lubrication
Nomenclature
Apparent contact area
Asperity contact area
Lubricated contact area
Cross sectional area of control volume
Ring axial face-width
Ring width in the radial direction (ring thickness)
Journal of Tribology. Received March 19, 2015;
Accepted manuscript posted October 15, 2015. doi:10.1115/1.4031780
Copyright (c) 2015 by ASME
Accepted Manuscript Not Copyedited
Downloaded From: http://tribology.asmedigitalcollection.asme.org/ on 10/16/2015 Terms of Use: http://www.asme.org/about-asme/terms-of-use

2
Young’s modulus of elasticity
Composite Young’s modulus of elasticity
Total friction
Boundary friction
Viscous friction
Total load on the ring
5/2
,
Statistical functions
Ring elastic (tension) force
Gas force acting behind the ring
Film shape
Maximum texture depth
Minimum film thickness
Texture profile
Profile of the compression ring
Piston top land to liner gap
Ring cross-sectional second moment of area
Ring peripheral length
Thickness of chevron leg
Piston top land height
Connecting rod length
Mass flow rate
Mass in a control volume
Gas pressure in combustion chamber /
Cavitation vaporisation pressure /
Elastic (tension) ring pressure /
Gas pressure behind the ring /
Journal of Tribology. Received March 19, 2015;
Accepted manuscript posted October 15, 2015. doi:10.1115/1.4031780
Copyright (c) 2015 by ASME
Accepted Manuscript Not Copyedited
Downloaded From: http://tribology.asmedigitalcollection.asme.org/ on 10/16/2015 Terms of Use: http://www.asme.org/about-asme/terms-of-use
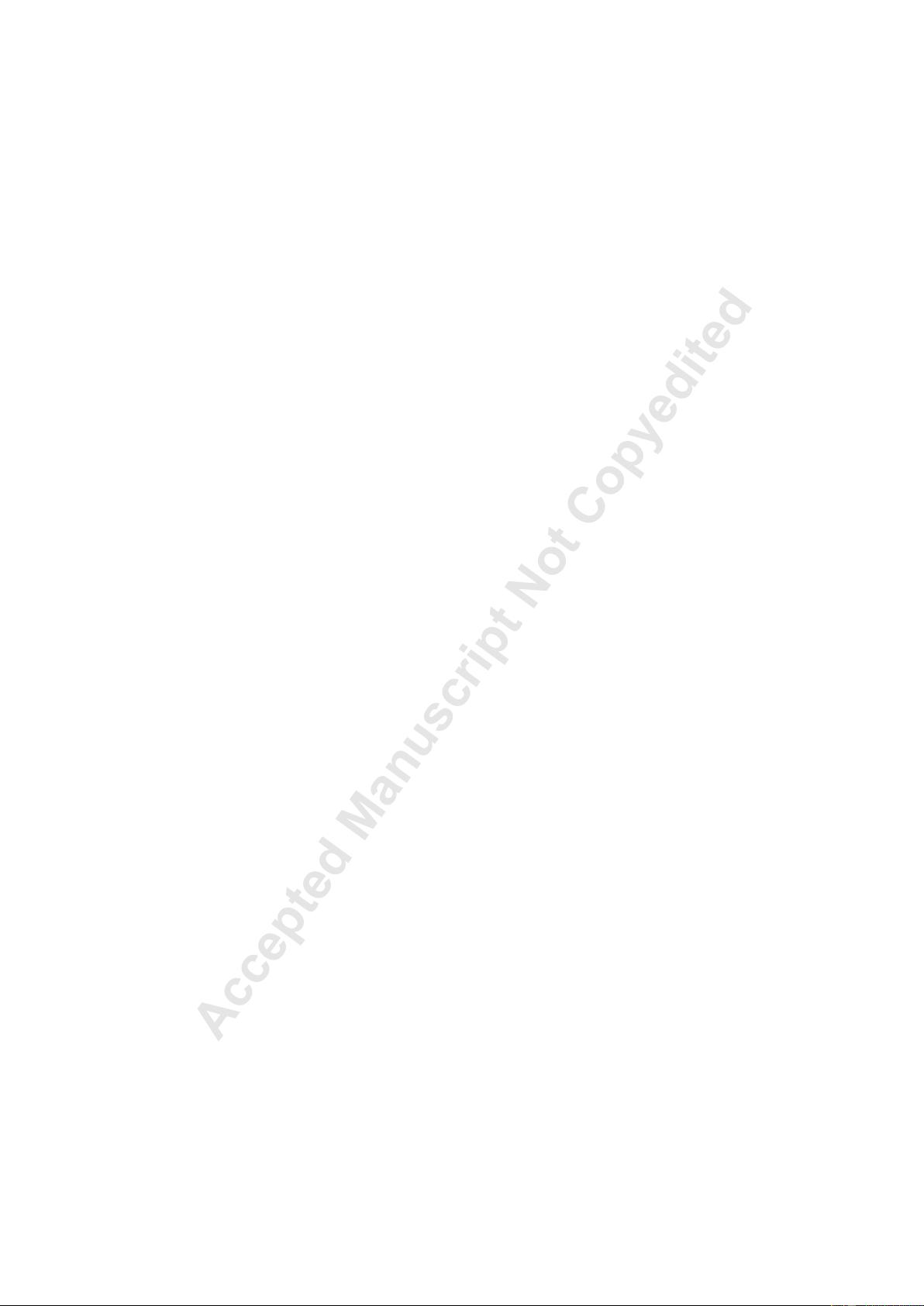
3
Hydrodynamic pressure /
Pressure on the lower ring face /
Pressure on the upper ring face /
Total frictional power loss
Crank-pin radius
Bore internal nominal radius
Bore top external radius
Specific gas constant .
Time
Sliding velocity /
Combustion chamber volume
Volume below piston ring and the second ring groove
Volume between piston ring and piston
Volume above top ring and combustion chamber
Engine displacement volume
Cylinder clearance volume
Velocity vector /
Contact load
Load share of the asperities
Hydrodynamic load carrying capacity
Direction along ring face-width (direction of lubricant entraining motion)
Axial position of lubricant film rupture
Centre-line of the chevron
Circumferential direction along ring face
Pressure-viscosity index
Greek symbols
Journal of Tribology. Received March 19, 2015;
Accepted manuscript posted October 15, 2015. doi:10.1115/1.4031780
Copyright (c) 2015 by ASME
Accepted Manuscript Not Copyedited
Downloaded From: http://tribology.asmedigitalcollection.asme.org/ on 10/16/2015 Terms of Use: http://www.asme.org/about-asme/terms-of-use

4
Piezo-viscous parameter
Thermo-viscous parameter 1
Ratio of specific heat capacities
Lubricant thermal expansion coefficient 1
Lubricant effective viscosity .
Lubricant viscosity at ambient conditions .
Viscosity of gas flowing from or to the combustion chamber .
Initial (bulk) lubricant temperature
Combustion chamber gas temperature
Initial assumed gas temperature at compression stroke
Effective lubricant temperature
Piston ring back temperature
Initial assumed gas temperature at power stroke
Temperature above top ring and combustion chamber
Average radius of curvature of asperities
Stribeck oil film parameter
Lubricant density
Lubricant density at ambient conditions
RMS roughness of contiguous surfaces
Number of asperities per unit contact area 1/
Viscous shear stress
Eyring shear stress
Adjusting numerical parameter
Crankshaft angular velocity /
1. Introduction
Fuel efficiency and reduction of emissions are key drivers for the modern automotive internal
combustion (IC) engine development. Parasitic frictional losses produced by the piston
Journal of Tribology. Received March 19, 2015;
Accepted manuscript posted October 15, 2015. doi:10.1115/1.4031780
Copyright (c) 2015 by ASME
Accepted Manuscript Not Copyedited
Downloaded From: http://tribology.asmedigitalcollection.asme.org/ on 10/16/2015 Terms of Use: http://www.asme.org/about-asme/terms-of-use

5
compression ring- cylinder liner contact account for 2-5 % of input fuel energy according to
Andersson [1]. With the increasingly stringent legislations, the adverse effect of emissions
mostly due to intrinsic inefficiency of IC engines and the growing scarcity of conventional
cheaper fuels, this level of parasitic loss from such a small conjunction is not sustainable.
In general, a significant effort is directed towards mitigating the parasitic losses, including the
associated errant dynamics. These include the pervading light-weight powertrain concept.
Other palliation routes include the lowering of lubricant viscosity, introduction of wear-
resistant and low friction coatings and surface texturing (e.g. Etsion and Sher [2] and Howell-
Smith et al [3]). All these palliative actions can introduce some drawbacks, such as excessive
ring dynamics, oil loss and blow-by (Tian et al [4] and Baker et al, [5]), reduced load carrying
capacity (particularly with the same engine oil in other higher loaded conjunctions such as the
cam-follower pair), as well as cavitation (Chong et al [6], Shahmohamadi et al [7]). Therefore,
analysis of compression ring–cylinder liner conjunction is a multi-variate and arguably one of
the most complex problems in tribo-dynamics.
The piston compression ring-cylinder liner contact experiences a transient regime of
lubrication due to the variable nature of contact kinematics and the applied contact load in the
various strokes of the IC engine. Therefore, a universally effective palliative measure for all
parts of the engine cycle and under various driving conditions cannot be assured. At piston
reversals (at the top dead centre, TDC and the bottom dead centre, BDC), there is momentary
cessation of lubricant entrainment into the contact. This combination invariably results in
mixed or boundary regimes of lubrication, where the direct contact of the surfaces at asperity
level is encountered. There is also significant ring elastodynamic behaviour in approaching
the TDC in order to seal the combustion chamber [8-9], this being the primary function of the
compression ring. In turn, the ideal conformance of the ring to the liner surface can result in
increased friction. In other instances during the piston cycle, mostly a hydrodynamic regime
of lubrication has been predicted and also noted through measurements [10-13]. These
observations, of course, are of a general nature as in reality the bore is not a right circular
cylinder as manufactured and fitted, and undergoes significant transient thermo-mechanical
distortions in service [14]. Therefore, the conjunctional gap between the ring and the liner
may experience a mixed regime of lubrication almost at any part of the cycle. However, in
general, worst tribological conditions are often encountered at TDC reversal, in transition
from the compression to the power stroke in a 4-stroke engine. This has been predicted
through numerous numerical analyses [1,2,6,7,10-14], which include varying degrees of
complexity, some of which have shown good agreement with the various experimental
measurements under different engine operating conditions [2,13].
Direct in-situ measurement of friction, using the floating liner method provides the best
opportunity for determination of friction under various engine running conditions [15-18].
Those reported by Gore et al [18] on a high performance motocross motor-bike engine
indicate that boundary interactions occur at the aforementioned TDC reversal and account for
a significant proportion of in-cycle frictional losses of ring-liner contact. Styles et al [19]
predict the same trend for a V12 high performance niche OEM vehicle, taking into account
precise measurement of physical, topographical and shear characteristics of coated surfaces,
Journal of Tribology. Received March 19, 2015;
Accepted manuscript posted October 15, 2015. doi:10.1115/1.4031780
Copyright (c) 2015 by ASME
Accepted Manuscript Not Copyedited
Downloaded From: http://tribology.asmedigitalcollection.asme.org/ on 10/16/2015 Terms of Use: http://www.asme.org/about-asme/terms-of-use