
MATERIALS AND MANUFACTURING PROCESSES
http://dx.doi.org/10.1080/10426914.2017.1317351
5 Ball-burnishing effect on deep residual stress on AISI 1038 and AA2017-T4
Andres Amador García-Granada
a
, Giovanni Gomez-Gras
b
, Ramón Jerez-Mesa
c
, J. Antonio Travieso-Rodriguez
d
, and
Guillermo Reyes
e
a
Universitat Ramon Llull. IQS School of Engineering, Industrial Engineering, Barcelona, Spain;
b
IQS School of Engineering/Universitat Ramón Llull,
Industrial Engineering, Barcelona, Spain;
c
Universitat Politecnica de Catalunya, Mechanical Engineering, Escola d’Enginyeria de Barcelona Est,
10 Barcelona, Spain;
d
Universitat Politècnica de Catalunya, Mechanical Engineering, Barcelona, Spain;
e
Universitat Ramon Llull. IQS School of
Engineering, Industrial Enginnering, Barcelona, Spain
Q1
ABSTRACT
Ball-burnishing induces compressive residual stresses on treated materials by the effect of plastic
deformation. The result is an increase in the fatigue life of the treated part, retarding the initiation of
cracks on the surface. Compressive residual stresses have been previously measured by X-ray diffraction
near the surface, revealing considerably high values at the maximum analyzed depth, in relation to other
finishing processes such as shot peening. However, the maximum analyzed depth is very limited by using
this technique. In this paper, the incremental hole drilling (IHD) technique is tested to measure residual
stresses, being able to reach a 2-mm measuring depth. To that objective, a commercial strain gage is used
and calibrated using finite element model simulations. A second FEM
Q2 based on material removal rate is
developed to obtain the equations to calculate the strain release through IHD. Finally, residual stresses
are measured experimentally with that technique on two different materials, confirming that ball-
burnishing increases the compressive residual stresses in layers up to 0.5 mm deep for the testing
conditions, which is a good response to industrial needs. The method proves to be suitable, simple and
inexpensive way to measure the value of these tensions.
ARTICLE HISTORY
Received 17 November 2016
Accepted 5 April 2017
KEYWORDS
Aluminum; burnishing;
drilling; element; finite; hole;
incremental; method;
residual; steel; stresses
Introduction
Current industry requires high-quality finishing of mechanical
40 parts to increase their fatigue resistance and achieve a low fric-
tion ratio. In this context, the relevance of surface integrity is
basic, so the development of finishing processes has become
one of the main drivers of industrial innovation worldwide.
In effect, they are responsible for the final residual stress state,
45 hardness and surface roughness conditions of parts, factors on
which fatigue life is dependent. These specific conditions can
be obtained through several processes, such as burnishing,
shot peening and electro-polishing. Shepard et al. [1] analyzed
the fatigue response on aeronautical Ti-6Al-4V specimens.
50 These pieces were subjected to three processes: ball-
burnishing, shot peening and electro-polishing. A comparative
analysis of their surface roughness was performed. Ball-
burnishing resulted in the lowest surface roughness (average
roughness R
a
≈ 3 µm), while electro-polishing and shot
55 peening resulted in R
a
≈ 17 µm and R
a
≈ 85 µm, respectively.
Ball-burnishing is considered a cold-working process,
during which elastic-plastic deformation is produced on the
workpiece because of the constant force transmitted by the
tool [2]. This operation is developed using a tool attached to
60 a CNCQ3 machine, applying a certain calibrated force to a
sphere. The sphere glides over the workpiece area, deforming
the peaks of the surface irregularities and flattening the
roughness profile, producing a much more regular surface.
The process is known for its positive effects on surface
65integrity. El-Axir et al. [3] proved the decrease in average
surface roughness of 2014 aluminum specimens, as the level
of cold work was increased by higher burnishing force and
number of passes. These positive results have also been proved
on concave and convex surfaces, as shown by Travieso-
70Rodriguez et al. (2011) on steel and aluminum workpieces
[4]. Secondly, surface hardness is enhanced by burnishing
due to cold work deformation, as shown by Prévey et al. [5]
on Ti-6Al-4V specimens. The same authors conclude that stress
introduced by burnishing reaches compressive values at depths
75higher than 1 mm. That result is confirmed by other authors,
such as Zhang et al. [6]. As a consequence, the wear resistance
of burnished materials is improved, which shows the compre-
hensive effects of burnishing as a finishing process (Hassan
et al.) [7], and a longer lifespan of industrial components can
80be expected, as explained by Hariharan and Prakash [8].
Many ball-burnishing tools exist in the market, such as the
ones commercialized by Mech-India Engineers [9] or Ecoroll
AG Werkzeugtechnik [10], and the one developed and
patented by Travieso-Rodriguez et al. [11].
85The ball-burnishing process has extensively been the object
of research activities addressing the optimization of process
parameters and the development of theoretical models. For
instance, Rodriguez et al. [12] published a model to optimize
ball-burnishing parameters, taking surface roughness and
CONTACT J. Antonio Travieso-Rodriguez antonio.travieso@upc.edu Universitat Politècnica de Catalunya, Mechanical Engineering, Av. d’Eduard
Maristany, 10-14, Barcelona, 08019 Spain.
Color versions of one or more of the figures in the article can be found online at www.tandfonline.com/lmmp.
© 2017 Taylor & Francis
3b2 Version Number : 11.0.3184/W Unicode (Apr 10 2014)
File path : P:/Santype(JATS)/Journals/TandF_Production/LMMP/v0n0/LMMP1317351/LMMP_A_1317351_J.3d
Date and Time : 26/4/17 and 15:47

90 residual stresses as response variables. Recent studies intro-
duce the assistance of vibrations in the process, revealing a
relevant improvement of results. Zhao et al. [13] applied
ultrasonic multi-roller burnishing on Ti-6Al-4V specimens,
observing a decrease of the material flow stress, which in turn
95 allows lower forces to be applied to achieve the same cold
work deformation and residual stresses. Travieso-Rodriguez
et al. [14] concluded that a ball-burnishing process assisted
by a 2-kHz vibration allows one to achieve similar results in
one pass, as opposed to five passes of the conventional process.
100 The results are confirmed on carbon steel specimens
(Travieso-Rodriguez et al.) [15].
Residual stresses can be measured through different meth-
ods, which can be classified according to the way they interact
with the tested material. A comprehensive review of residual
105 stress measurements methods is explained at Withers and
Bhadeshia [16,17]. Methods involving material loss are known
as destructive methods. An example of a totally destructive
method is explained by Garcia-Granada [18,19]. If the material
is locally removed, although not compromising the structural
110 integrity of the component, these methods are referred to as
semi-destructive. Two good examples are deep hole drilling
and incremental hole drilling (IHD) [20,21]. In contrast, non-
destructive methods do not affect the integrity of the tested
part, using the diffraction of neutrons according to Maawad
115 et al. [22] or X-ray diffraction [14,15,23–25] to estimate
near-surface residual stresses. The major drawback of this
diffraction method is the low depth to which compressive
residual stresses measurements can be performed. For this rea-
son, IHD is tested as an alternative method to measure
120 residual stresses in burnished specimens, able to reach deeper
layers.
The IHD method is a well-known and common technique
to evaluate residual stresses at any position of the surface of a
workpiece up to a depth of around 2 mm [26,27]. The
125 maximum measurable depth depends on the selected strain
gage rosette, and is defined at the E837-08 ASTM standard
[28]. There are many ways to analyze strain release during
IHD, as summarized by Ajovalasit et al. [29]. In order to
estimate the error of measuring residual stresses near the yield
130 stress value, finite element simulations can be carried out
in order to adapt the testing parameters to that condition
[30–32]. Gharbi et al. [33] showed the effect of the ball-
burnishing force on residual stress on the surface of AISI
1010. Zemčík et al. [34] measured the same on EN 10132–4
135 specimens. Abdulstaar et al. [35] showed the fatigue improve-
ment on Al6082 for both shot peening and ball-burnishing
with compressive residual stresses up to 0.5 mm below the
surface but without describing the directionality of residual
stresses and the method used to measure them.
140 This paper has two objectives. The first one is to demon-
strate that ball-burnishing is a successful process in introdu-
cing compressive residual stresses in layers a few millimeters
below the surface. This verification is basic to validate the
ball-burnishing process to treat industrial parts subjected to
145 fatigue working regimes during their lifespan.
The second one is to validate the IHD method to measure
compressive residual stresses of the burnished parts, by
comparing it to the X-ray diffraction results available and
developed by other authors [14,15]. IHD has not been exten-
150sively applied to assess the effects of ball-burnishing at deep
layers of the material because its application is more difficult
than X-ray diffraction. Nevertheless, it is a cheaper method,
and allows one to perform measurements at higher depths
of the treated part, that is, to assess in a more comprehensive
155way the effects of plastic deformation derived from
ball-burnishing.
Materials and Methods
Four specimens of AA2017-T4 aluminum and four specimens
of AISI 2038 steel were tested. The most relevant properties for
160both materials are shown in Table 1. The samples were pre-
pared through an initial face milling using a CNC milling
machine and an 80-mm-diameter plate tool mill with five
inserts. Cutting parameters were 3000 min
1
of cutting speed,
a feed rate of 1000 mm/min and 0.5 mm of depth of cut. After
165that, they were subjected to a ball-burnishing operation, using
the tool designed by Gómez-Gras et al. [36] (Fig. 1), equipped
with a 10-mm-diameter burnishing ball. Different forces were
applied for both treated materials, with 90 N being the
nominal force for aluminum and 110 N for steel. The feed
170velocity was 600 mm/min and one pass was performed along
every burnishing path. These values were selected based on
the results obtained in different experimental research, accord-
ing to Travieso-Rodriguez et al. [6].
The burnished specimens were then equipped with a strain
175gage rosette to measure the induced residual stresses effect of
the burnishing force. The chosen rosette was the 1-RY21-3/120
(RY21 henceforth) from HBM
Q4. For this rosette, the mean
diameter of the strain gages is D ¼13 mm, larger than
that defined as type A in the ASTM E837-08 standard [28].
180The main reason for using such a large rosette is because it
allows one to measure residual stresses down to deeper layers
of the material. The minimum recommended thickness of
the specimen is 1.2D ¼15.6 mm, condition satisfied by using
40-mm-thick specimens. Strain gage ε
1x
was always aligned
185with the ball-burnishing direction, as shown in Fig. 2(a).
The rosette was then connected to a Spider 8 data acquisition
device.
To perform the burnishing experiments, a simple CNC was
programmed and implemented in an Odisea CNC machine
190operated by a Fagor 8055 controller, as shown in Fig. 2(b).
This CNC machine was used to perform the stepped drill
required for the measurement, using a 5-mm-diameter drill,
inside the admissible interval (4.751, 5.385) defined at the
ASTM standard, dependent of the rosette diameter. The
195incremental drilling procedure is described in the standard
as a process in which successive drills are performed until
reaching the maximum depth, increasing each time the depth
Table 1. Properties of materials used for both workpieces.
Material
d
[kg/m
3
]
r<rtb>
##ffi#y [MPa]
r<rtb>
##ffi#u [MPa]
ε<rtb>
##ffi#f [%] E [GPa] ν[-]
2017-T4
aluminum
2.8 275 427 22 72.4 0.33
AISI 2038
steel
7.8 285 515 18 200 0.29
2 A. A. GARCÍA-GRANADA ET AL.
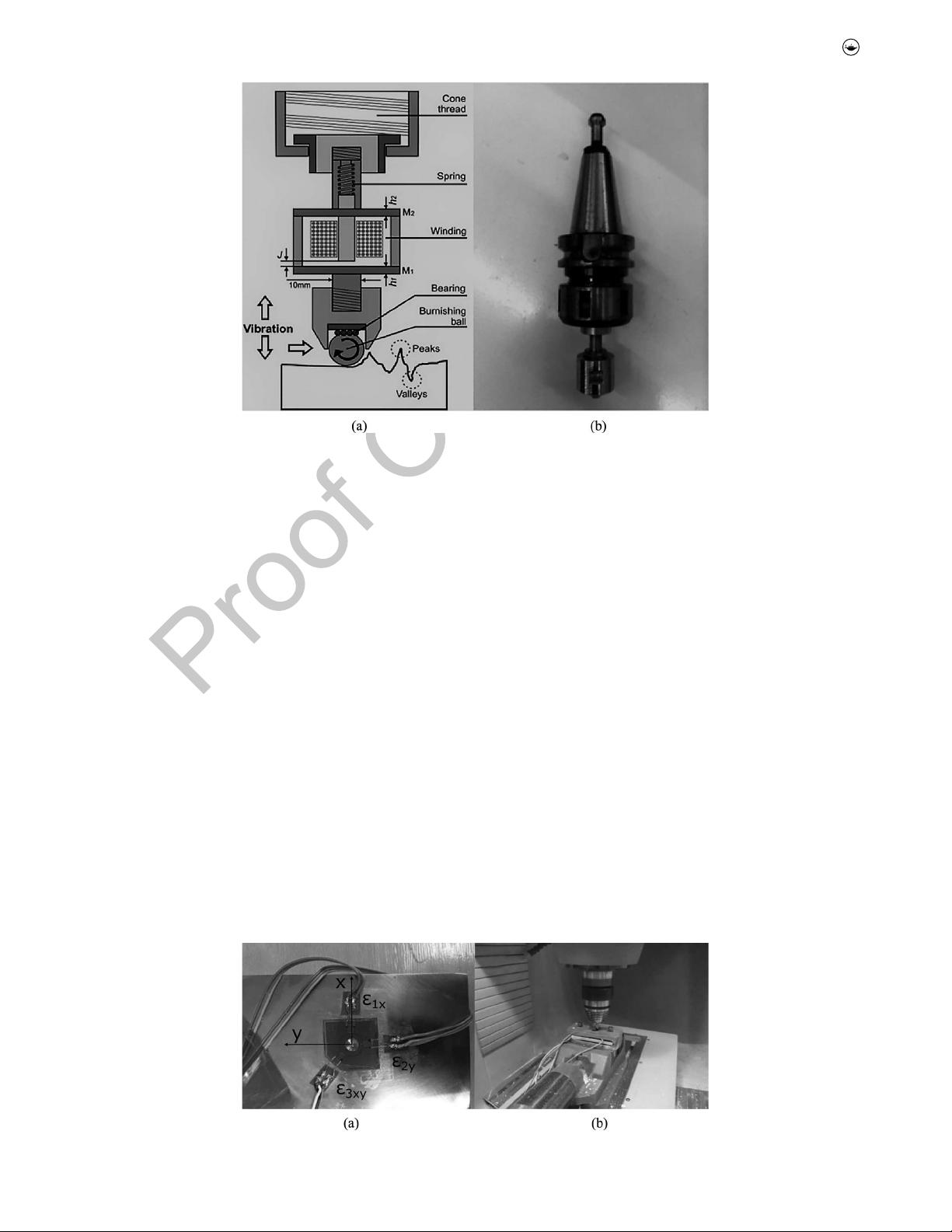
of cut by 0.13 mm. In this case, lower steps of 0.05 mm were
used to obtain a more accurate strain relaxation profile as a
200 function of the depth. Such small increments were also used
in the FEM calibration of parameters to obtain residual
stresses from released strains.
Rosette RY21 is not calibrated in the ASTM E837-08
standard, but the standard states that calibration matrixes for
205 other rosettes can be obtained by adjusting D and the hole
diameter to the main parameters. In this case, certain
parameters are applied to obtain nonuniform residual stress
distributions with those given for a rosette of D ¼ 5.13 mm,
with a hole diameter of 2 mm and steps of 0.05 mm. Following
210 this rule, the maximum measured depth was 2.534 mm,
coinciding with the objective range of residual stresses to be
measured. The final hole depth specified in the standard should
be around 0.4D ¼5.2 mm for thick workpieces with uniform
residual stresses. In order to obtain a proper matrix component
215 for RY21 finite elements simulations were carried out.
This paper shows two different finite element models to
validate the experimental drilling method for the burnished
parts. The first one, as already explained, allows one to cali-
brate the RY21 rosette, as it is not calibrated at the reference
220ASTM standard. The objective of the second one is to correct
the eccentricity between the drill and the center of the rosette.
This correction is necessary because too high deviations could
lead to erroneous results.
The strategy of using a large strain gage rosette in combi-
225nation with small depth increase between drilling steps to
obtain deeper and more accurate residual stresses requires
the generation of a corrective matrix of coefficients. This
approach was already taken by Schajer and Steinzig, and
Montay et al. to measure the residual stress of shot peened
230parts [37,38], and Sedighi and Mahmoodi for angular rolling
[27]. Niku-Lari et al. [39] found the calibration matrix for
an RY21 rosette using steps of 0.01 mm and 4- and 5-mm
drills. Unfortunately, the matrix parameters were not provided
in the paper.
235First, a simple simulation applying a constant pressure, p, to
calculate a
i
is required. A second simulation applying a cyclic
pressure p·cos(2h) and shear pressure p·sin(2h) is required to
obtain b
i
. These simulations are performed for each drilling
step. This means that, to achieve a total depth of 5 mm in steps
240of 0.05 mm, 100 geometrical models must be created, and two
different simulations must be run for each one.
Figure 1. Ball-burnishing tool used in the experiments. (a) Schematic representation. (b) Real device.
Figure 2. (a) 1-RY21-3/120 strain gage rosette set up on a ball-burnished specimen. (b) Fixation of specimen on Odisea CNC with controller Fagor 8055 for
incremental hole drilling.
MATERIALS AND MANUFACTURING PROCESSES 3
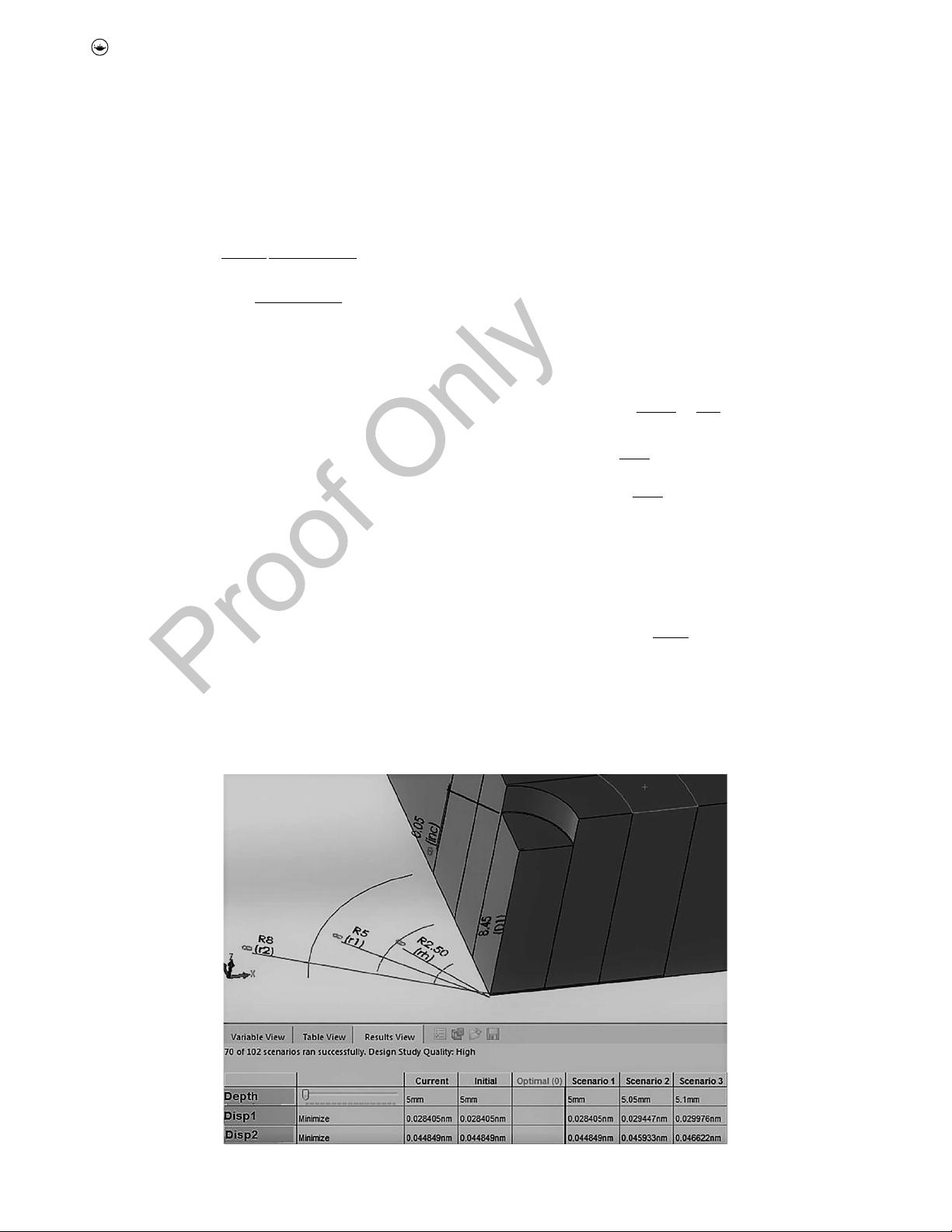
To perform this iterative calculation, a parametric model
was built in SOLIDWORKS. A total of 200 simulations were
executed, and the results were collected through a link between
245 the parametric model in SOLIDWORKS and a datasheet in
EXCEL. Equation (1) shows an expression given by Montay
et al. [38], with a correction for depth step by Sedighi and
Mahmoodi [27] and Niku-Lari et al. [39] and a correction in
strain gages definition by Xiao et al. [40].
a
in
¼
2E
1 tð Þ
U
2
U
1
2p r
2
r
1
ð ÞDh
ð1Þ
b
in
¼ 2E
U
2
U
1
2p r
2
r
1
ð ÞDh
ð2Þ
where U are the values of nodal displacement, r
1
is the mini-
mum radius position and r
2
is the maximum radius position.
250 In the case of the RY21 rosette, r
1
¼5 mm and r
2
¼8 mm,
which means that D ¼r
1
þr
2
¼13 mm, as explained above.
Sub-index i refers to the ith layer, out of a total of n layers
throughout the total thickness, Δh.
Figure 3 shows the parametric model drawn in
255 SOLIDWORKS, including the radius of the drilling hole,
r
h
¼2.5 mm, and an increase step of 0.05 mm between the
layers.
The mesh size was set to 0.05 mm at the edge of the hole,
evolving to 0.5 mm at remote points. The model was
260 composed of 202,064 tetrahedral solid elements. Once all the
simulations were carried out, the parameters were obtained
and fitted to a curve as a function of drilling depth. These
fitted curves would eventually allow using different steps to
speed up the IHD measurement process. Parameters and
265 curve fitting are shown in Fig. 4 for the first 2 mm of depth
to obtain a good curve fitting in the area where residual stress
measurements need to be assessed.
The estimation of a and b obtained from this FEM model
is in agreement with those reported by similar studies
270[27–29,38–40]. Nevertheless, the ASTM standard suggests that
all hole and stress depths should be multiplied by 13/5.13 to
take into consideration the change in the rosette diameter,
and also by (5/2)
2
to take into consideration the change in
the drill diameter. Such correction is plotted in Fig. 4 to show
275that when different rosettes are considered, this approximation
is not good enough, as there are many parameters that chan-
ged from the calibrated data.
A device has been designed to introduce 4-point bending
loads on aluminum plates (65 59 5 mm), in order to vali-
280date experimentally the measurement procedure, proposed in
the previous subsection (Fig. 5).
Two forces P are applied on the specimen through each
screw of the device. The consequent stress and deflection at
each specimen section can be calculated by Eqs. (3) and 4,
285respectively.
r xð Þ
a<x<L a
¼
Pah=2
I
¼
6Pa
bh
2
¼ 0:048P MPa½ ð3Þ
d xð Þ
a<x<L=2
¼
Pa
6LEI
L xð Þ L
2
L xð Þ
2
að Þ
2
þ
Pa
6LEI
x L
2
x
2
a
2
ð4Þ
where a is the loadspan, h is the height, b is the width, L is the
length of the specimen and I is the moment of inertia.
290The maximum force to be applied to achieve the yield stress
is given by Eq. (5).
Pmax ¼
r
x
bh
2
24 a
¼ 4447:9 N ð5Þ
Equations (3) and (4) can be verified using simulations of
295the 4-point bending device where 1000 N forces are applied.
Around 48 MPa of stress is expected. Figure 6 shows the com-
parison between experimental and theoretical stress results,
Figure 3. Parametric model in SOLIDWORKS to obtain a and b parameters.
4 A. A. GARCÍA-GRANADA ET AL.

demonstrating that the used method is adequate although a
slight deviation is observed in the first 0.3 mm.
300 A second application of FEM simulations is necessary to
estimate the errors introduced by the drill eccentricity with
respect to the rosette center, as reported by several authors
such as Svarıcek and Vlk [41], Ghasemi and Mohammadi
[42] and Schuster and Gibmeier [43]. This step is recom-
305 mended, for the standard sets a maximum eccentricity of
0.004D ¼0.052 mm.
A simulation of the material removal process is performed
to obtain the released strains as during the IHD measurement.
The main objective is to validate the a and b parameters with
310 the real measured residual stresses. The FEM is developed
using ABAQUS, comprising a first step to introduce a residual
stress in the specimen, and subsequent phases modeling the
IHD measurement itself. The initial coarse mesh size was set
to 0.5 mm in all directions, with depth steps of 0.5 mm up
315to a maximum depth of 5 mm. In order to drill 2 mm just four
points at depths of 0.5, 1.0, 1.5 and 2.0 mm are obtained.
Finally, the fine mesh size was set to 0.05 mm at each layer
to be removed during the drilling operation. In this way, the
first layer of 0.05 mm was removed in step 2. Each layer was
320removed in subsequent steps, until reaching a maximum
2 mm depth corresponding to step 41. At a distance of
0.5 mm from the edge of the hole, a transition to a 0.5 mm
mesh was established, thus creating 82032 solid elements.
On the other hand, the residual stresses introduced during
325step 1 were combinations of uniaxial compression (r
x
¼ 1,
r
y
¼0), biaxial compression (r
x
¼ 1, r
y
¼ 1) and a
combined compression state (r
x
¼ 1, r
y
¼ 0.8). All stress
units are in MPa.
The redistribution of residual stress is shown in Fig. 7 for
330different mesh sizes and stress states. As reported by Ajovalasit
et al. [29] and Beghini et al. [26], plasticity during hole drilling
should be taken into account, as the equations for strain
release assume elastic material behaviour. However, Ajovalasit
Figure 4. Fitted curve for the estimation of a and b parameters as a function of depth.
Figure 5. Device to perform the 4-point bending test, to validate the residual
stress measurements.
Figure 6. Experimental validation of the stress calculation through the
developed strain gage method.
MATERIALS AND MANUFACTURING PROCESSES 5