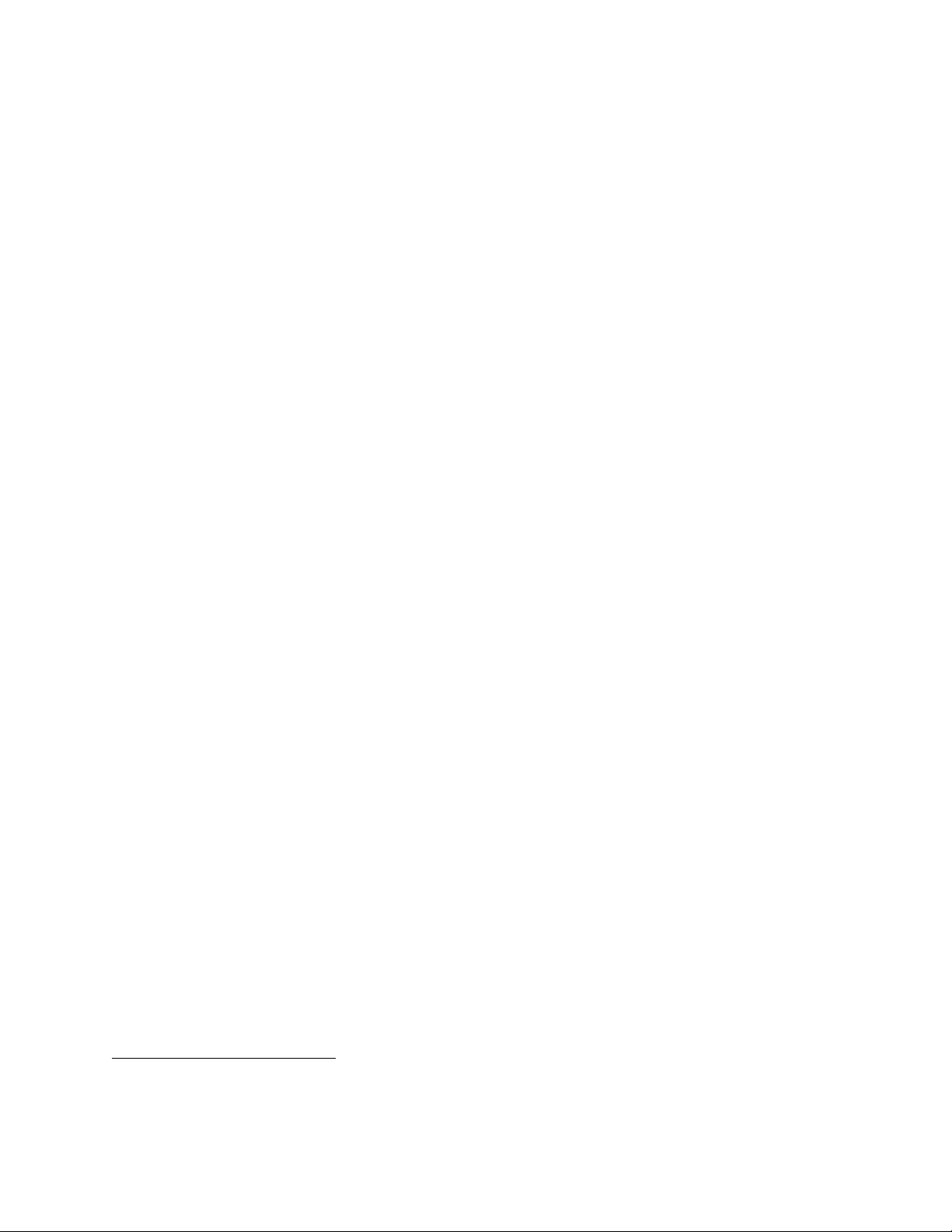




read more
Pitch effector can be made of low temperature tolerance material: Because only cold fan air impinges on it, the pitch effector does not have to be made of high temperature tolerant materials.•
Since the top of the fan nacelle is likely to have laminar flow over at least a portion of it, while the fuselage that is being covered is where the turbulent boundary layer is thickest, a increasing fan nacelle length might actually decrease drag.
Minimal engine core jet noise: Designing to a low turbogenerator nozzle pressure ratio extracts the maximum amount of energy from the gas stream which has the effect of reducing the turbogenerator exhaust gastemperature and velocity and hence reduces noise.
Possible non-linear aircraft control laws: Being embedded in the boundary layer may cause interactions between the external aerodynamics and the propulsion system.•
The use of electrical power transmission allows a high degree of flexibility in positioning the turbogenerators and fan modules to best advantage.
The speed of the power turbine shaft in the turbine engine is independent of the fan shaft speed - the electrical system functions as a gearbox with an arbitrary gear ratio.
Power inverters are required to allow the speed of the fans to be reduced to match the available power while the power and speed of the remaining turbogenerator are brought to a maximum.•
The authors feel that for large transport aircraft it will be necessary to use superconducting motors and generators rather than conventional motors and generators in the aircraft propulsion system to reduce the weight fraction of the propulsion system.
The turbogenerators could be oversized with regard to the power needs of propulsion to provide significant amounts of electrical power for non-propulsion uses while in flight.
Rerunning the propulsion system performance study with a lower 0.943 freestream to fan face pressure ratio may result in generally higher TSFC values and a higher optimum FPR.
Greater pitch effector effectiveness: Blowing all the fan air over the pitch effector increases its effectiveness, allowing the pitch effector to be smaller and/or not located as far aft.•
For the purposes of calculating the cooling required, the authors have assumed a power loss of 0.03% total for the entire superconducting portion of the electrical system.
using a distributed turboelectric propulsion system with superconducting devices may present adverse effects in overall vehicle performance and operation.
To match the inlet mass flow rate and inlet ram drag entering the fan face at the vehicle ADP condition and to account for total pressure loss due to boundary layer build-up along airframe surface at the inlet lip location, a 1st order approximationof the boundary layer profile was obtained using simple flat plate equivalent of upper airframe surface by matching assumed total pressure loss of N2A configuration and mass flow rate entering the current N3-X inlet.
The generators, motors, inverters, and the balance of the superconducting system may weigh more than a mechanical gearbox that accomplishes some of the same tasks as the turboelectric system.•
If turbogenerator noise remains too high for an exposed mounting location, the turbogenerator can readily be moved elsewhere on the aircraft without disturbing the fan nacelle location or operation.•
the higher losses for the embedded installation compared to a pylon mount with a pitot inlet means that the bottom of the TSFC curve for embedded engines is likely to be at a higher FPR than for a podded, pylon mounted engine.
Given this loss level, the methane flow rate required for cooling is approximately 17% of that required to fully power the aircraft with methane.
The several types of AC losses that occur in HTS materials can be reduced by reducing the size of HTS filaments in the composite conductor and twisting them.