
1178 IEEE TRANSACTIONS ON NEURAL NETWORKS, VOL. 13, NO. 5, SEPTEMBER 2002
A CMOS Feedforward Neural-Network Chip
With On-Chip Parallel Learning for Oscillation
Cancellation
Jin Liu, Member, IEEE, Martin A. Brooke, Member, IEEE, and Kenichi Hirotsu, Member, IEEE
Abstract—This paper presents a mixed signal CMOS feedfor-
ward neural-network chip with on-chip error-reduction hardware
for real-time adaptation. The chip has compact on-chip weighs ca-
pable of high-speedparallel learning;the implemented learning al-
gorithm is a genetic random search algorithm—the random weight
change (RWC) algorithm. Thealgorithm does not require a known
desired neural-network output for error calculation and is suit-
able for direct feedback control. With hardware experiments, we
demonstrate that the RWC chip, as a direct feedback controller,
successfully suppresses unstable oscillations modeling combustion
engine instability in real time.
Index Terms—Analog finite impulse response (FIR) filter, direct
feedback control, neural-network chip, parallel on-chip learning,
oscillation cancellation.
I. INTRODUCTION
O
RIGINALLY, most neural networks are implemented
by software running on computers. However, as neural
networks gain wider acceptance in a greater variety of applica-
tions, it appears that many practical applications require high
computational power to deal with the complexity or real-time
constraints. Software simulations on serial computers cannot
provide the computational power required, since they transform
the parallel neural-network operations into serial operations.
When the networks become larger, the software simulation
time increases accordingly. With multiprocessor computers,
the number of processors typically available does not compare
with the full parallelism of hundreds, thousands, or millions
of neurons in most neural networks. In addition, software
simulations are run on computers, which are usually expensive
and cannot always be affordable.
As a solution to the above problems, dedicated hardware is
purposely designed and manufactured to offer a higher level of
parallelism and speed. Parallel operations can potentially pro-
vide high computationalpower at a limited cost, thus, can poten-
tially solve a complex problem in a short time period, compared
Manuscript received October 25, 2000; revised July 20, 2001 and January 24,
2002. This work was supported by the Multidisciplinary University Research
Initiative (MURI) on Intelligent Turbine Engines (MITE) Project, DOD-Army
Research Office, under Grant DAAH04-96-1-0008.
J. Liu is with the Department of Electrical Engineering, the University of
Texas at Dallas, Richardson, TX 75080 USA.
M. A. Brooke is with the Department of Electrical and Computer Engi-
neering, Georgia Institute of Technology, Atlanta, GA 30332 USA.
K. Hirotsu is with the Sumitomo Electric Industries, Ltd., Osaka 541-0041,
Japan.
Publisher Item Identifier S 1045-9227(02)05565-0.
with serial operations. However, reported implementations of
neural networks do not always exploit the parallelism.
A common principle for allhardware implementationsis their
simplicity. Mathematical operations that are easy to implement
in software might often be very burdensome in the hardware
and therefore more costly. Hardware-friendly algorithms are es-
sential to ensure the functionality and cost effectiveness of the
hardware implementation. In this research, a hardware-friendly
algorithm, called random-weight-change (RWC) algorithm [1],
is implemented on CMOS processes. The RWC algorithm is a
fully parallel rule that is insensitive to circuit nonidealities. In
addition, the error can be specified such that minimizing the
error leads the system to reach its desired performance and it
is not necessary to calculate the error by comparing the ac-
tual output of the neural network with the desired output of the
neural network. This enables the RWC chip to operate as a di-
rect feedback controller for real-time control applications.
In the last decade, research has demonstrated that on-chip
learning is possible on small problems, like
XOR problems. In
this paper, a fully parallel learning neural-network chip is ex-
perimentally tested to operate as an output direct feedback con-
troller suppressing oscillations modeling combustioninstability,
which is a dynamic nonlinear real-time system.
II. I
SSUES ON THE DESIGN OF LEARNING
NEURAL-NETWORK HARDWARE
Neural networks can be implemented with software, digital
hardware, or analog hardware [2]. Depending on the applica-
tion nature, cost requirements, and chip size limitations due to
manufacturability, each ofthe implementation techniqueshas its
advantages and disadvantages. The implementations of on-chip
learning neural-network hardware differ in three main aspects:
the learning algorithm, the synapse or weigh circuits, and the
activation function circuits.
A. Learning Algorithm
The learning algorithms are associated with the specific
neural-network architectures. This work focuses on the widely
used layered feedforward neural-network architecture. Among
the different algorithms associated with this architecture,
the following algorithms have been implemented in CMOS
integrated circuits: the backpropagation (BP) algorithm, the
chain perturbation rule, and the random weight change rule.
The BP algorithm requires precise implementation of the
computing units, like adders, multipliers, etc. It is very sen-
1045-9227/02$17.00 © 2002 IEEE
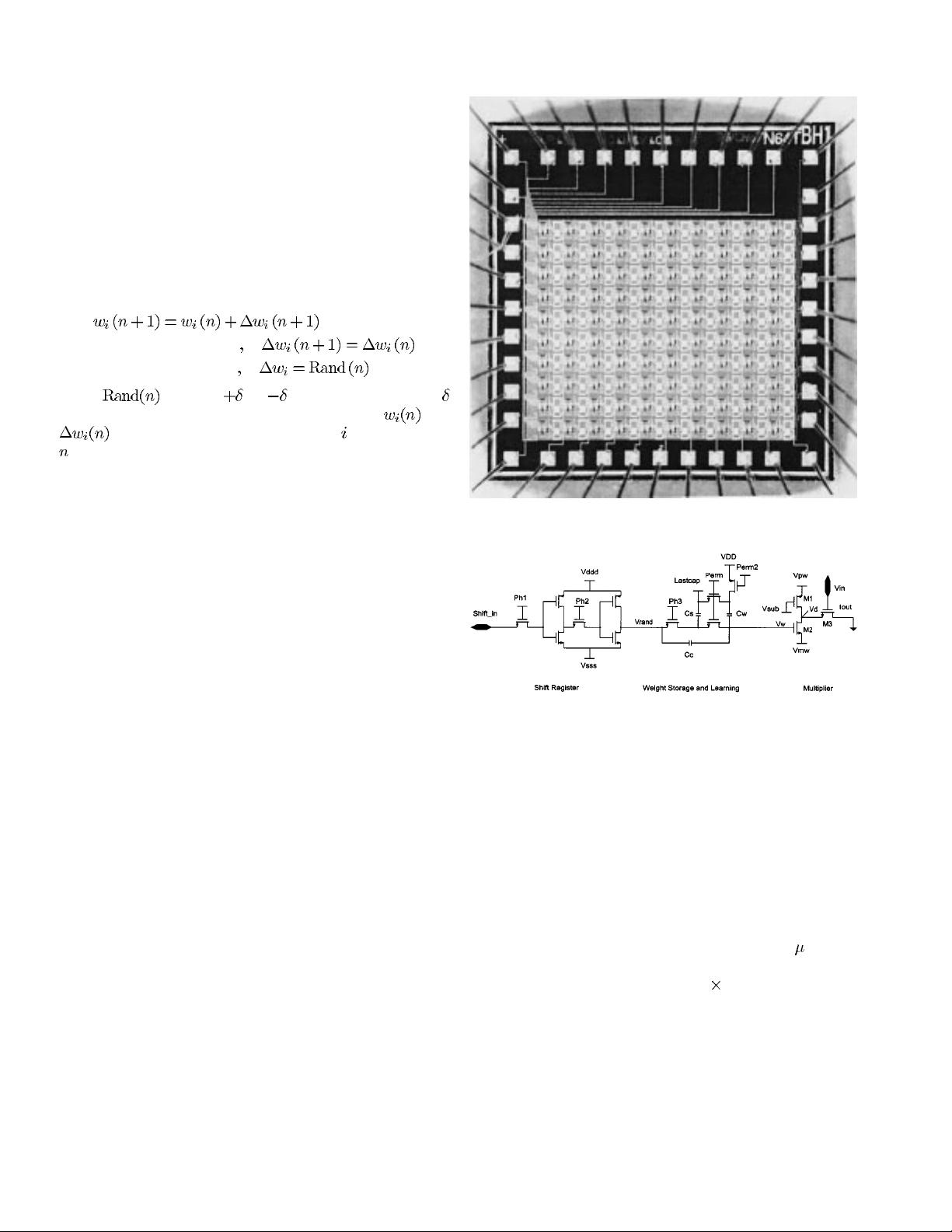
LIU et al.: A CMOS FEEDFORWARD NEURAL-NETWORK CHIP 1179
sitive to analog circuit nonidealities, thus, it is not suitable
for compact mixed signal implementation. Learning rules like
serial-weight-perturbation [3] (or Madaline Rule III) and the
chain perturbation rule [4] are very tolerant of the analog circuit
nonidealities, but they are either serial or partially parallel
computation algorithms, thus are often too slow for real-time
control. In this research, we use the RWC algorithm [1], which
is a fully parallel rule that is insensitive to circuit nonidealities
and can be used in direct feedback control. The RWC algorithm
is defined as follows.
For the system weights
If the error is decreased
If the error is increased
where is either or with equal probability,
is a small quantity that sets the learning rate, and and
are the weight and weight change of th synapse at the
th iteration. All the weights adapt at the same time in each
weight adaptation cycle.
Previously, it has been shown with simulations that a modi-
fied RWC algorithm can identify and control an inductor motor
[5]. Further simulation-based research has shown that the RWC
algorithm is immune to analog circuit nonidealities [6]. An ex-
ample of analog circuit nonidealities is the nonlinearity and
offset in the multiplier, as will be shown in the following sec-
tion. Replacing the ideal multiplier with the nonlinear multiplier
constructed from the measurement result of an integrated cir-
cuit implementation of the multiplier, we redo the simulations
on identifying and controlling an inductor motor. The results of
both conditions are almost identical, with minor difference in
initial the learning process [6].
B. Synapse Circuits
Categorized by storage types, there are five kinds of synapse
circuits: capacitor only [1], [7]–[11], capacitor with refreshment
[12]–[14], capacitor with EEPROM [4], digital [15], [16], and
mixed D/A [17] circuits.
Capacitor weights are compact and easy to program, but
they have leakage problems. Leakage current causes the weight
charge stored in the capacitor to decay. Usually, the capacitors
have to be designed large enough (around 20 pF for room
temperature decay in seconds) to prevent unwanted weight
value decay. Capacitor weights with refreshment can solve
leakage problem, but they need off chip memory. In addition,
the added A/D and D/A converters either make the chip large or
result in slow serial operation. EEPROM weights are compact
nonvolatile memories (permanent storage), but they are process
sensitive and hard to program. Digital weights are usually large,
requiring around 16-bit precision to implement BP learning.
The mixed D/A weight storage is a balanced solution when
permanent storage is necessary.
For this research, the chip is to operate in conditions where
the system changes continuously and so weight leakage prob-
lems are mitigated by continuous weight updates. Thus, the chip
described here uses capacitor as weight storage. The weight re-
tention time is experimentally found to be around 2 s for loosing
1% of the weight value at room temperature.
Fig. 1. Chip photo.
Fig. 2. Schematic of a weight cell.
C. Activation Function Circuits
Research [11], [18] shows that the nonlinearity used in
neural-network activation functions can be replaced by multi-
plier nonlinearity. In this work, since the weight multiplication
circuit has nonlinearity, we uses a linear current to voltage
converter with saturation to implement the activation function.
III. C
IRCUIT DESIGN
A. Chip Architecture
The chipwas fabricatedthrough MOSIS inOrbit 2-
m n-well
process. Fig. 1 shows a photomicrograph of the 2 mm on a side
chip. It contains 100 weights in a 10
10 array and has ten
inputs and ten outputs. The input pads are located at the right
side of the chip, and the output pads are located at the bottom
side of the chip. The pads at the top and left sides of the chip are
used for voltage supplies and control signals. This arrangement
makes it possible for the chip to be cascaded into multilayer
networks.
The schematic of one weight cell is shown in Fig. 2. The left
part is a digital shift register for shifting in random numbers.
The right part is a simple multiplier. The circuits in the middle
are the weight storage and weight modification circuits.

1180 IEEE TRANSACTIONS ON NEURAL NETWORKS, VOL. 13, NO. 5, SEPTEMBER 2002
Fig. 3. HSPICE simulation result on the adjustment of a weight value.
The shift registers of all the cells are connected as a chain,
therefore, only one random bit needs to be fed into the chip at
a time. At a given time, each cell sees a random number at the
output of the shift register, being either “1” or “0.” If it is “1,”
the voltage
is equal to ; if it is a “0,” the voltage is
equal to
.
B. Weight Storage and Adaptation Circuits
The weight charge is stored in the larger capacitor
, with
representing the weight value. Switching clock Ph3 on,
while clock perm is off, loads the smaller capacitor
with a
small amount of charge. Then, connecting
in parallel with
the smaller capacitor
changes the weight value. Suppose
that the voltage across
is and the voltage across is
before connecting them in parallel, after connecting them
in parallel for charge sharing, the final voltages across them
are the same, supposed to be
. The total charge carried
over the two capacitors does not change,
, thus the new voltage across ,
will be
.
In this implementation, the
is 100 times of , thus
. So, every time, the weight value
changes approximately by 1% of the voltage across
.How-
ever, the change is nonlinear, due to the weight decay term,
in the above equation. The bottom plate of will be
charged to
, which will be either or . The top
plate of
is connected to a bias voltage Lastcap. The values
of
, and Lastcap together control the step size of
weight change. The
is an external biasing to set the range
of the actual weight value, which is the sum of the value of
and the charge across . Clock perm2 has a complementary
phase of clock perm.
An individual weight will have its value either increased or
decreased every time the clock Ph3 is activated. When the data
shifted into the weight cell is a “1” (5 v), the weight is increased;
and when the data shifted in is a “0” (0 v), the weight is de-
creased. Fig. 3 shows the results of an HSPICE simulation of
the weight changing with time. In the simulation, from the time
0 to 200 ms, a series of “1s” are shifted into the cell. Clock Ph3
is activated to allow the random number to be added to the per-
manent weight change; clock perm turns on and off to make
permanent change on the weight value. Clocks Ph3 and perm
have complimentary phases with period of 2 ms. As a result, the
weight keeps on incrementing for 100 times during the 200 ms
period. From time 200 to 400 ms, a series of “0’s” are shifted to
the cell, so the weight keeps on decrementing. The same process
repeats for several cycles in the simulation. The first two cycles
Fig. 4. Measured result on the adjustment of a weight value.
are shown in the figure, the rest of the cycles are identical to the
second cycle.
The weight increment and decrement rates are determined by
the values of
, and Lastcap, as mentioned earlier. In
this simulation,
is 5 V, is 0 V, and Lastcap is 2.5
V. When a “0” is shifted in,
equals to 0 V; when a “1”
is shifted in,
equals to 5 V. However, the voltage at the
bottom plate of
does not always equal to exactly, due
to the NMOS switching gate controlled by Ph3, which is 5 V.
Suppose the threshold voltage of the switching gate is 0.7 V, the
voltage at the bottom plate of
equals to 4.3 V when
equals to 5 V, and equals to 0 V when equals to 0 V. Thus,
the increment step is approximately 0.018 V while the decre-
ment step is 0.025 V, corresponding to about 7
-bit resolu-
tion.
Fig. 4 shows the measurement result of the weight increment
and decrement, for comparison with the simulated result shown
in Fig. 3. The shift
in data are series of “0s” and “1s.” In this
measurement, the three voltages controlling the weight incre-
ment and decrement step size are adjusted so that the up slope
and the down slope are almost symmetrical.
The following scheme implements the RWC learning. If the
calculated error decreases, clocks Ph1 and Ph2 stop. The same
random number, representing the same weight change direction,
will be used to load
with the charge, thus, the weights change
in the same direction. If the error is increased, clocks Ph1 and
Ph2 are turned on, a new random bit will be shifted in, resulting
a random change of the weight values.
C. Multiplier Circuits
The operation of the multiplier, whose schematic is shown in
Fig. 2, is as follows. The voltage
is the substrate voltage,
which is the most negative voltage among all the biasing volt-
ages. In the simulation and experiments, we use complimentary
power supplies, i.e.,
. The output of the multi-
plier is a current flowing into a fixed voltage, which should be

LIU et al.: A CMOS FEEDFORWARD NEURAL-NETWORK CHIP 1181
Fig. 5. HSPICE simulation result on the multiplication function.
Fig. 6. Measured result on the multiplier output current range.
in the middle of and ; in this case, it is ground. The
weight voltage
is added at the gate of M2. Fig. 5 shows the
HSPICE simulation result of the multiplier. The horizontal axis
is the input voltage
, the vertical axis is the output current
, and different curves represent different weight voltage
values
. The multiplier attempts to produce a multiplying
relationship as follows:
. When is about 2
V, the drain of M2
is about 0 V; when is below 2 V,
is positive and when is above 2 V, is negative. The range
of
is small to ensure that M3 is operated in the nonsaturation
region, thus the output current of M3 is approximately propor-
tional to drain-source voltage,
. Depending on the polarity
of
, the output current can flow in both directions and is
defined as follows:
where is the threshold voltage of M3. The above equation
explains why the simulated multiplier has both offset and non-
linearity. The nonlinear relationship is actually desirable as it
eliminates the need for a nonlinear stage following the multi-
pliers, as discussed earlier.
Hardware test results, presented in Fig. 6, show that the mea-
sured multiplier function is close to the HSPICE simulation re-
sult. The two lines are constructed from the measured points
when the weight is programmed to be at its maximum and min-
imum. The horizontal axis is input voltage, with units of V and
the vertical axis is current, with units of
A.
IV. L
EARNING PROCESS
In the learning, a permanent change is made every time a new
pattern is shifted in. If the change makes the error decrease,
the weights will keep on changing in the same direction in the
following iterations, until the error is increased. If the change
Fig. 7. Test setup for the inverter experiment.
makes the error to increase, the weights keep this change, and
try on a different change for the next iteration.
The test setup shown in Fig. 7 is used to demonstrate the
random-weight-change learning process. The task is to train a
two-input–one-output network to implement an inverter. It is
configured so that one input is always held high as the reference,
while the second one alternates between high and low. The de-
sired output is the inverse of the second input.
In the test, the high and low are set to two voltage values for
the networkoutputs to reach.The network thenis trained tomin-
imize an error signal, which is calculated as follows. Suppose
that the desired output values of high and low are
and ,
and the actual output values of high and low are
and , the
error is calculated as
.
Thus, when the error is small enough, the network implements
an inverter. The error is not calculated on current chip. Rather,
it is calculated on PC in the test setup and is sent to the chip, as
a 1-bit digital signal. However, the error calculation can be in-
corporated on the same chip, with additional digital circuits for
error calculation.
The desired low and high output voltages, in this experiment,
are 1 and 2 V. So, the desired output should oscillate between 1
and 2 V. Fig. 8 shows a typical initial learning process captured
from the oscilloscope. The figure shows that, within 0.8 s, the
network is trained to behave as an inverter with the specified
high and low output voltages.
After the initial training, the network convergesto the inverter
function. Then, the network tries to maintain the performance
as an inverter by continuously adjusting itself. Fig. 9 shows a
100-ms time slice of the continuously adjusting process; the de-
sired high and low output voltages are 1.5 and 0.5 V for this
case. There are two signals in the plot. One of them is the ph2
clock, which is represented by the spikes shown in the figure.
A high of ph2 means that a new random number is sifted in
and indicates that the error starts to increase. The other signal
is the inverter output. It oscillates between high and low, since
the input alternates between low and high. The two horizontal
markers indicate the desired high and low voltages.
Starting from point A (time 0), indicated by the trigger arrow,
clock ph2 is high, thus, a new random pattern is introduced.
From point A to point B, the output signal oscillates between
high and low, converging to the desired high and low values.
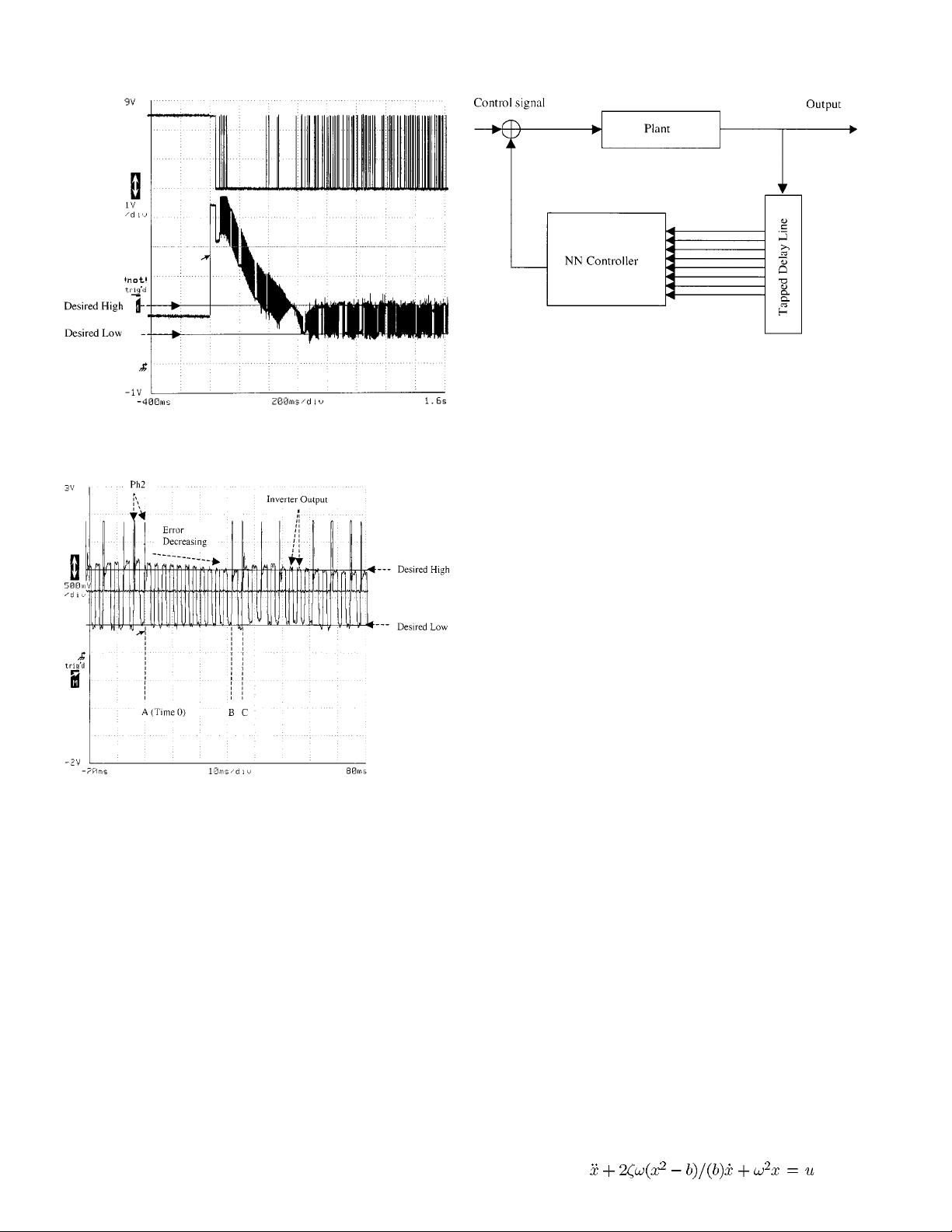
1182 IEEE TRANSACTIONS ON NEURAL NETWORKS, VOL. 13, NO. 5, SEPTEMBER 2002
Fig. 8. Oscilloscope screen capture of the initial learning process for the
inverter experiment, with the desired low and high voltages as 1 and 2 V.
Fig. 9. Oscilloscope screen capture of the detailed learning process of the
inverter experiment.
According to the error calculation equation, the error decreases.
During this process, clock Ph2 stops to let the network keep
on using the weight change, which is consistent with the algo-
rithm. The error decreases until point B, when the error starts
to increase. Thus, the network stops using this weight change
direction and tries a new pattern, indicated by a spike of ph2 at
point B. Unfortunately, this pattern cause the error to increase;
the network gives up this direction pattern and tries a new one,
indicated by another spike at point C. As this process goes on,
the network dynamically maintains its performance as an in-
verter by continuously adjusting its weights.
The above experimental results show that the recorded
hardware learning process complies with the random weight
change algorithm and the weights of neural-network chip can
be trained in real time for the neural network to implement
simple functions. Next, we apply the chip to a more compli-
cated application—direct feedback control for combustion
oscillation cancellation.
Fig. 10. Direct feedback control scheme with a neural-network controller.
V. C OMBUSTION INSTABILITY AND
DIRECT
FEEDBACK CONTROL
The combustion system is a dynamic nonlinear system, with
randomly appearingoscillations of differentfrequencies and un-
stable damping factors. When no control is applied, this system
is unstable and eventually reaches a bounded oscillation state.
The goal of the control is to suppress the oscillation. There are
several well-known passive approaches for reducing the insta-
bilities [19], [20]. However, the implementation of such passive
approaches is high cost and time consuming, and they often fail
to adequately damp the instability. The effort of developing ac-
tive control systems for damping such instabilities has increased
in recent years. Since the combustion system is a nonlinear
system, the system parameters vary with time and operating
conditions. The active controllers that developed to suppress the
oscillation in fixed modes cannot deal with the unpredicted new
oscillation modes. In addition, the actuation delay presented in
the control loop also causes difficulties for the control.
In this research, we use the neural-network chip for direct
feedback control [21] of the oscillation. The RWC chip has
on-chip learning ability; the weights on the chip are adjusted in
parallel, which enables the chip to adapt fast enough for many
real-time control applications. The adaptation time of each
weight update is about 2 ns. Fig. 10 shows the direct feedback
control scheme with the neural-network chip as controller. The
tapped delay line in control setup is used to sample the plant
output (combustion chamber pressure). In general, a period of
the plant output of the lowest signal frequency is to be covered.
At the same time, the sampling rate of the tap delay line should
also be faster than the Nyquist sampling rate of the highest
frequency component of the plant output. The rule is that the
neural network should be provided enough information on
the plant dynamics. Software simulation [22], [23], using the
setup in Fig. 10, suggests that it is possible to suppress the
combustion oscillation with the direct feedback control scheme
using the neural-network controller with the RWC algorithm.
A. Combustion Model With Continuously Changing
Parameters
In this simulation, the combustion process is modeled by the
limit cycle model:
, where